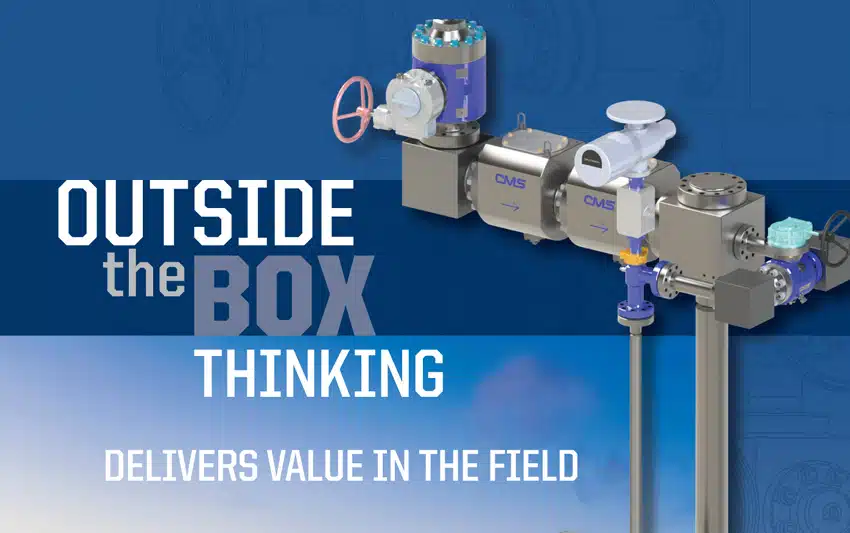
Conquering Unique Demands of the Offshore Environment with Custom, Value-Driven Manifold and Piping Solutions
The quest for the optimum solution is always the objective of oil and gas producers and their respective engineering companies when evaluating designs for new facilities or upgrading existing facilities. This endeavor inevitably involves both technical and economic considerations. Although most engineers will express some ‘out of the box’ ideas, they more often than not fall back on tried and tested solutions.
During this quest for optimum solutions, many oil and gas producers have attempted to incorporate ‘lessons learned’ thinking into project development in an effort to predict, avoid or remedy field problems that typically occur during commissioning, startup and operation of their facilities. However, in most cases, these remedies remain with the operating personnel and do not generate the changes in corporate standards, which engineering companies continue to rely upon during project execution.
Since its founding in January 2004 as a design, manufacturing, sales and service organization specializing in upstream oil and gas flow control applications, CORTEC has been at the forefront of ‘thinking out of the box’ and applying ‘lessons learned’ into the approach to both valve/choke designs as well as many of the systems into which these products are installed. Over the following 15+ years, the experienced team of valve manufacturers would go on to expand CORTEC’s operations to encompass a broad range of product lines and turnkey designs. Today, all manner of valve types, from compact isolation valves, conventional flanged end valves, check valves and a range of choke models can be combined into high quality, value-adding turnkey systems.
Smaller and Lighter: The Benefits of a Compact Design
CORTEC designs many systems that add capability to new and existing facilities with significant space restrictions, such as production platforms acquiring new subsea tiebacks or deepwater drill ships introducing new managed pressure drilling (MPD) systems on deck. CORTEC excels in applications with high-pressure designs up to API 20,000 pressure class, non-standard material requirements, critical service valves, corrosive or erosive service conditions, etc. CORTEC offers a line of equipment suited to a wide variety of uses, and excels in providing solutions to customers’ specific project needs. Typically, CORTEC meets with the operator’s engineering design team very early in the process in order to formulate a design plan that will maximize weight and space savings for the client’s specific application. By maintaining a high level of involvement from the start, CORTEC is able to enhance not only the valves, but each individual flow line component within the system.
CORTEC specializes in delivering high-pressure piping within the guidelines of industry manufacturing standards but in dimensions lightweight and compact enough to enable the equipment to occupy a minimal footprint in the field. The benefits of this approach include the ability to host a system that physically fits in a limited environment, with a high level of quality and performance along with long-term reliability.
CORTEC’s system designs average between 35-50% space and/or weight reduction when compared to other OEM conventional designs. CORTEC developed a high flow rate system for a drillship capable of flowing up to 2,000 GPM while maintaining flow velocities less than 20 fps. In one recent GOM production platform manifold design, CORTEC saved a major end user more than 88 tons of additional weight by utilizing its compact valves for a production manifold compared with a competitor’s standard product offering. In both instances these concepts were taken from initial engineered concept to a delivered product solution within the client’s project timeline constraints.
Identifying Unique Demands of the Offshore Environment
In 2010, CORTEC began working with two leading oil and gas producers in the Gulf of Mexico to help them resolve operational problems with process valves on their offshore facilities. During this effort, it became obvious that most of the valve-related issues were not due to any particular supplier, but rather to the specifications to which the valves were manufactured. The specifications were corporate standards, which had been developed over decades for onshore process facilities and did not take the offshore environment into consideration. Repairing or replacing an onshore valve was immensely easier and far less costly than an offshore valve. This difference was not reflected in the specification for offshore valves. Additionally, as the operating pressures increased, valve design specifications did not follow with increased conservatism. It was easier for corporate staff to merely apply the same design specs originally written for Class 150 valves to the higher pressures up to 20,000 psi. Something needed to change.
A company decision was made to develop a valve design that would meet the conservatism necessary to minimize, if not eliminate, the field problems associated with offshore facilities. Additionally, CORTEC wanted to create an ‘out of the box’ design for the most critical valves in offshore application — the Boarding Shutdown Valves (BSDV) — for which gate valves are traditionally used. BSDVs are the first valves in production lines coming onto a GOM platform and therefore the most critical valve on the platform. The U.S. government has stringent requirements for these valves, which include requiring a third-party API 6AV1 certification and testing in the field every 30 days to guarantee zero leakage. If they fail the test, the well is required to shut in until the cause of the leak is corrected. CORTEC’s experience in meeting API 6AV1 test requirements has provided insight into many of the field problems associated with valves used in oil and gas production. In this case, considerable upgrades were made to CORTEC’s standard Compact Ball Valve to allow the company to challenge conventional gate valves for the BSDV. The upgraded design was the first ball valve to pass the API 6AV1 sand slurry test globally.
CORTEC has had more than five years of operational experience in BSDV service. These valves are tested monthly per BSEE 30 CFR 250 Sub H to ensure they retain tight shutoff. In one particular project, CORTEC provided a custom API 10K – 8 in. double isolation and bleed assembly complete with bypass and instrumentation in less than 20 weeks to replace leaking gate valves for a major oil and gas producer in the Gulf of Mexico. The CORTEC compact valve design saves 35-50% of the space and weight compared to conventional ball or gate valve designs. The higher the pressure or the larger the size, the greater the savings achieved. In high pressure piping (10,000 – 20,000 psi) there are no industrial standards for pipe accessories, which means that leaving the fabrication of these elements to a fab yard is problematic. Once CORTEC had an ‘out of the box’ compact ball valve design that could also solve many of the ‘lessons learned’ valve related issues, CORTEC went a step further and designed compact piping accessories (elbows, tees, spools, blocks, etc.) in accordance with API standards that enables it to supply complete compact piping/manifold systems. The systems can provide huge space and weight savings (up to 70%).
Closer Look: CORTEC’s GOM Production Platform Manifold Design
Extending its ‘out of the box’ approach, CORTEC incorporated its upgraded compact valve with its compact choke and choke relief valves (CRV) into complete MPD systems. Today, CORTEC is considered the premier supplier of turnkey manifolds and solutions for offshore MPD systems. A project to deliver a turnkey manifold system took place in 2014, when two major E&P companies were on a joint venture to lease out a drillship for a GOM campaign. CORTEC was approached with a basic piping schematic that was designed around 8 in. piping with 6 in. orifice chokes and 4 in. orifice CRVs desired to accommodate high flow rates up to 2000 GPM. At that time, a system that size had never been developed and some valve models in those sizes were not commercially available.
Furthering the complications, there wasn’t a lot of available spacing on the vessel to accommodate such a system. Existing conventional drilling systems needed to be tied in and the vessel involved was not originally designed to have permanent MPD systems. The customer’s desired path was to utilize an open area that was very narrow at 11 ft wide and ran along a railing of the moonpool. Opposite to the moonpool was a forklift alley that was spaced with support columns for the rig decks. The head spacing was fully utilized at 7 ft and hosted various piping runs for miscellaneous rig functions such as fire suppression lines.
CORTEC took a 3D scan of the spacing and the customer’s functional P&ID to bring the project to life. The design required all custom piping and new valve models with larger internal trim diameters to match the client’s specification. There were 36 weeks from the initial approved conceptual layout to a delivered system. A project of this scale can be considered a massive undertaking and there are few (if any) companies operating today that could undertake a challenge to this extent and deliver so quickly. All of these designs complied with API 6A PSL 3 requirements and were third party reviewed for compliance to ABS CDS throughout the design and manufacturing process.
Since that time, CORTEC has become the dominant supplier of MPD chokes through its CX family of drilling chokes. To date, CORTEC has outfitted more than a dozen major deepwater drilling vessels with similar systems, with each crafted to suit specific client preferences and to work with each vessel’s unique spacing constraints.
Liason with User and EPC
One of the most difficult tasks CORTEC has faced is communicating the message to users and engineers on the economic value of the ‘out of the box’ and ‘lessons learned’ experience. When approached with an ‘out of the box’ product, the first thing engineers say is that it is too different from current norms and therefore out of their comfort zone. On the ‘lessons learned’ product, the reaction is that it requires changes to corporate specs that are too difficult to achieve. Both of these views are short sighted. To achieve the maximum result in the most economical package for 20-30 years of operational use, there needs to be dialog between the user, EPC and the supplier of key equipment. This conversation needs to include not only original cost but also the long-term operational (maintenance) cost. It is understood that there is a difference between capital and maintenance budgets, but there has to be a compromise when it comes to the best specification for a product or system. CORTEC enjoys sharing the information and experience it has accumulated with users and EPCs on valve, choke and system design to enable them to take advantage of ‘out of the box’ and ‘lessons learned’ developments.
Conclusion
The types of jobs that CORTEC takes on span many of the product lines that CORTEC offers, including compact isolation valves, chokes and a full range of API flowline components. There is a great degree of convenience for clients in working with a manufacturer who can provide a turnkey solution that is managed in-house from start to finish. From the engineering design through delivery, as the sole or primary vendor, CORTEC has complete control of the build quality, dimensional tolerances, production and delivery schedule, and any other complications that may typically be encountered when utilizing the services of multiple vendors. This unique blend of flexibility and capability has allowed CORTEC to bring tremendous value to many projects, paving the way for long lasting relationships with CORTEC’s clients.
About CORTEC
Today, the CORTEC brand is comprised of two globally operating divisions, CORTEC Fluid Control (CFC) and CORTEC Manifold Systems (CMS). CFC manufactures an extensive line of production and drilling chokes for a wide array of applications along with a line of Choke Relief Valves CRVs, API flowline components and turnkey valve manifold packages. CMS provides a complete line of high end compact valves designed and manufactured according to precise project specifications, including trunnion and floating ball valve designs, as well as compact check and diverter valves. CMS specializes in combining considerable engineering and manufacturing resources to offer clients full turnkey valve manifold packages for production, drilling and service applications. CORTEC’s divisions hold the appropriate quality accreditations to meet or exceed the requirements of the American Petroleum Institute (API) Specifications 6A, 6D and 16C. The CORTEC quality program is registered in accordance with ISO 9001 International Quality Management Standard and API Q1.